Jeden z największych, pierwszomontażowych dostawców części samochodowych ma kilka centr badawczo-rozwojowych w Polsce. Jedno z nich znajduje się we Wrocławiu, w którego regionie mieszczą się także trzy zakłady produkcyjne. Wrocławscy inżynierowie mogą pochwalić się szczególnym osiągnięciem. Platforma hamulcowa mBSP XBS, wykorzystywana przez wiodących producentów pojazdów ciężarowych to w dużej mierze ich dzieło.
Wizyta we wrocławskiej fabryce ZF CV Systems
Grupa ZF ma wieloletnie doświadczenie w opracowywaniu systemów dla pojazdów użytkowych. Po przejęciu firmy WABCO, koncern jeszcze bardziej rozszerzył swoje kompetencje, a wiele działów, które dotychczas pracowały odrębnie w ramach dwóch niezależnych firm, zaczęło tworzyć synergię. Miejscem szczególnym na mapie posiadającego swoje oddziały na całym świecie koncernu, jest Wrocław. Po zakończeniu procesu łączenia dywizji ZF i WABCO, w mieście tym oraz jego okolicach znajdują się łącznie trzy zakłady produkcyjne grupy i centrum inżynieryjne, związane z rynkiem pojazdów użytkowych. Odwiedziliśmy jeden z nich.
Zakład ZF CV Systems Poland, mieszczący się przy ul. Aleksandra Ostrowskiego we Wrocławiu funkcjonuje od 2001 r. Był obiektem należącym do firmy WABCO. Zmiany właścicielskie, które sprawiły, że amerykańska marka znalazła się w grupie ZF, zakończyły się w 2020 r. Kompetencje firmy zostały poszerzone, gdyż ZF miało w swoim asortymencie produkty dla pojazdów ciężarowych, których w portfolio nie miało WABCO. W 2022 r. powołano do życia dywizję Commecial Vehicle Solutions, która stała się największym na świecie dostawcą komponentów i systemów dla branży pojazdów użytkowych. Jej lokalizacje w Polsce (w ramach spółki ZF CV Systems Poland) dają pracę ok. 2850 osobom, łącznie zajmując 53 tys. mkw.
Wrocławska fabryka, którą mieliśmy okazję zwiedzić posiada własny dział badawczo-rozwojowy (R&D), w którym pracuje aż 480 osób. 3500 tys. mkw. to przestrzeń wykorzystywana przez laboratoria i stanowiska testowe. Tych jest łącznie 100, w tym aż 70 komór temperaturowych i klimatycznych, umożliwiających symulację pracy podzespołów w pojeździe w różnych warunkach i regionach świata. Przeprowadza się tu testy mechaniczne, elektromechaniczne i elektroniczne. Wrocławski dział R&D pracuje nie tylko nad rozwojem produktów, wytwarzanych we Wrocławiu, ale nad projektami rozwojowymi w ramach całej globalnej sieci Grupy ZF.
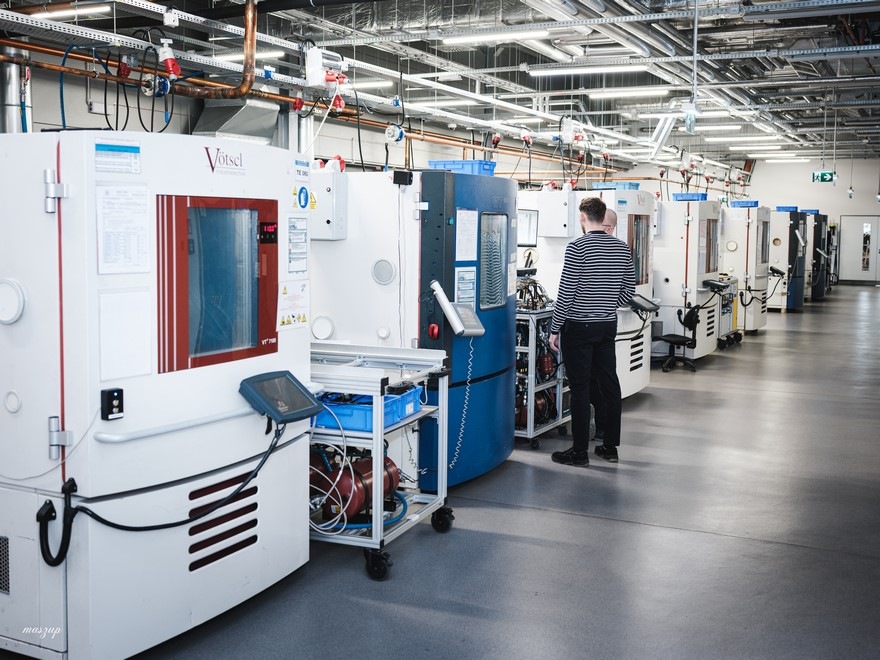
– Nasi inżynierowie we Wrocławiu mają znaczący wkład w rozwój technologii ZF w zakresie układów hamulcowych, zawieszenia pneumatycznego czy komponentów sprzęgieł i skrzyń biegów do pojazdów użytkowych. – powiedziała dr Elżbieta Gawin, dyrektorka Zespołu R&D ZF CV Systems Poland. – Nasza współpraca z globalną siecią inżynieryjną ZF oraz z lokalnym zakładem produkcyjnym daje nam szansę zaangażowania się w procesy rozwoju produktu od pomysłu, przez testowanie, aż po produkcję najnowszych technologii dla pojazdów użytkowych.
Mimo globalnego charakteru pracy, wrocławski dział badawczo-rozwojowy przydaje się lokalnie. W fabryce implementowane są nowe rozwiązania, które mają dać firmie przewagę na wielu polach związanych z produkcją podzespołów.
– Implementujemy nowoczesne narzędzia cyfrowe, które ułatwiają pracę naszym pracownikom. Kształcimy zespół w zakresie cyfrowych kompetencji, co pozwala na szybszą analizę i reakcję. Wśród naszych innowacji znajduje się Digital Twin, który w przyszłości umożliwi nam elastyczne wprowadzanie zmian i optymalizację procesów produkcyjnych, zapewniając jednocześnie najwyższe standardy jakościowe i technologiczne. – powiedział Sebastian Gałka, Site Leader ZF CV Systems Poland we Wrocławiu
Digital Twin to nic innego jak tworzenie cyfrowej kopii podzespołu, umożliwiającej przeprowadzenie niektórych implementacji czy testów w środowisku wirtualnym. Znacznie przyspiesza to proces od projektu do finalnego wdrożenia produktu i obniża jego koszty. Inżynierowie ZF zgodnie twierdzą, że tworzenie „cyfrowych bliźniaków” to prawdziwy „game changer” w branży produkcji części motoryzacyjnych. Umożliwia jednak nie tylko wdrażanie nowych rozwiązań w obszarze produkcyjnym, ale także przeprowadzanie symulacji odzwierciedlających zachowania produktu w okresie jego życia.
ZF CV Systems Poland – co produkuje fabryka?
Poza działem badawczo-rozwojowym, zakład przy ulicy Ostrowskiego prowadzi także działalność produkcyjną. Powstają tu zarówno konwencjonalne, jak i niekonwencjonalne systemy hamulcowe, a także elementy do pneumatycznych układów zawieszenia samochodów osobowych. Jeden z pilotażowych projektów realizowanych we Wrocławiu dotyczy zaworu ABS, będącego integralną częścią platformy hamulcowej mBSP XBS. W okolicy Wrocławia, w Krajkowie znajduje się także fabryka REMAN, zajmująca się regeneracją części.
Pneumatyczna platforma hamulcowa nowej generacji ZF mBSP XBS
Oczkiem w głowie wrocławskiej jednostki ZF jest nowa platforma hamulcowa mBSP XBS, która umożliwia elektronicznie sterowane, pneumatycznie uruchamiane hamowanie i nadaje się do wszystkich konfiguracji pojazdów użytkowych, w tym ciężarówek i przyczep. W porównaniu do EBS, czyli poprzedniego systemu oferowanego przez producenta, w mBSP XBS zredukowano liczbę komponentów o 30%. System jest łatwiejszy do montażu w pojeździe, gdyż zawiera mniej składników, które łącznie zajmują mniej miejsca. Poprzedni system zawiera 6 elementów, z których każdy musiał być oddzielnie programowany. Nowy system to tylko 4 podzespoły, które zarządzane są tylko przez jedną centralną jednostkę (ECU). Platforma jest modułowa i skalowalna, co pozwala ZF odpowiedzieć na potrzeby producentów pojazdów. Zapewnia skalowalne funkcje od ABS po EBS, jednocześnie obsługując funkcje automatyzacji jazdy do poziomu 5.
Przejęcie WABCO przez ZF nie zakończyło drogi rozwoju tego producenta, kojarzonego od dekad z produkcją podzespołów do pojazdów ciężkich. Nie każdy wie, że to WABCO było pierwszą firmą, która wdrożyła system hamulcowy zapobiegający blokowaniu kół (ABS) do ciężarówek i przyczep (już w 1981 r.). Z kolei w 1996 r. WABCO zaprezentowało elektroniczny układ hamulcowy EBS i adaptacyjny tempomat. W 2001 r. miała miejsce premiera onGuardMAX – systemu ostrzegającego kierowcę ciężarówki przed zbliżającą się kolizją. System umożliwia autonomiczne zahamowanie pojazdu w razie potrzeby. Nowy układ hamulcowy mBSP XBS to dowód na to, że połączenie kompetencji WABCO i ZF pozwoli na jeszcze szybsze i sprawniejsze opracowywanie innowacji, przeznaczonych do pojazdów ciężarowych. Cieszy fakt, że w tej dywizji tak dużą rolę odgrywają polskie jednostki, takie jak wrocławskie fabryki i centra badawczo-rozwojowe.
Komentarze